The Insulation
Every type of container has a barrier, and every barrier has insulating properties. Insulation is what slows down the temperature transfer between the product and the environment. A glass bottle hardly registers on the insulation scale. Meanwhile the insulation in a jacket made for the summit of Mt. Everest is probably some of the best. So the questions are, how good is the insulation and what does it matter in cold chain management?
Insulation is assigned an R-value (a measure of how well a barrier resists heat flow). The higher the R-value, the better it insulates. In cold chain management the idea is to keep the product at a desired temperature. When using containers for transport and/or storage of temperature sensitive product, the better the container’s R-value, the longer it will keep ambient temperatures (conditions outside the container…hot or cold) away from the product inside the container. Not only does a better R-value increase hold time, it leads to a more consistent, uniform temperature throughout the container.
There are two ways to increase the R-value of a barrier: add more material (thicker) or change the material (type). Adding thickness to a container is easy and the most common go-to method of DIYers. It works, but it usually adds unnecessary bulk to the container and reduces the container’s capacity. Changing the type of insulation is a bit harder as material knowledge is needed. That, combined with an added cost, usually is the limiting factor of this solution. Yet, having a cold chain management transporter with the largest R-value possible is paramount for the safety and efficacy of what it carries. Here are some insulation types…
Cardboard/Plastic – The most basic type of insulation is a thin wall of plastic or cardboard. Generally this material is less than 1” thick and barely provides any thermal protection, although it is cheap. Using this as your only insulation is a big no-no in cold chain management. Temperature sensitive product closest to the walls will quickly have excursions, and the rest will soon follow as the R-value is close to nothing.
Polystyrene – The most common type of insulation is polystyrene. This is your typical white foam that may or may not have a hard plastic shell around it. Typically found in off-the-shelf coolers at big-box retailers, this type of insulation provides basic protection, but not for long periods of time (and it’s not considered environmentally friendly). Some advantages include being lite weight, low cost, and shock absorbent.
Polyurethane – Higher-end coolers are now utilizing polyurethane as it adds both strength and R-value. Applications demanding rugged use (hunting, fishing, etc.), without the worry of added bulk or weight, are quickly making this type of insulation the mainstream of mid to high-end coolers. Although not considered environmentally friendly, long hold-times (with walls over 2” thick) make these types of coolers attractive to outdoor enthusiasts.
Aerogel – Found in flexible applications, aerogels are considered high-performance insulators but have yet to make it into the cooler market. Costly to make, this insulation is durable and easy to work with, but doesn’t surpass the performance of polyurethane enough to outweigh the cost differential.
Vacuum Insulated Panel – At 5-10 times the R-value of polyurethane, this ultra-insulation vacuum insulated panel (VIP) is the best thermal protector currently being made. A 1” thick panel (used in all Cool Cube™ PCM coolers) has the thermal performance of 7” of expanded polystyrene or 4.5” of polyurethane. This leads to the product being protected from outside conditions for a longer duration, a significantly better size to capacity ratio, and a more consistent internal temperature throughout. The drawback is that it is more expensive to make.
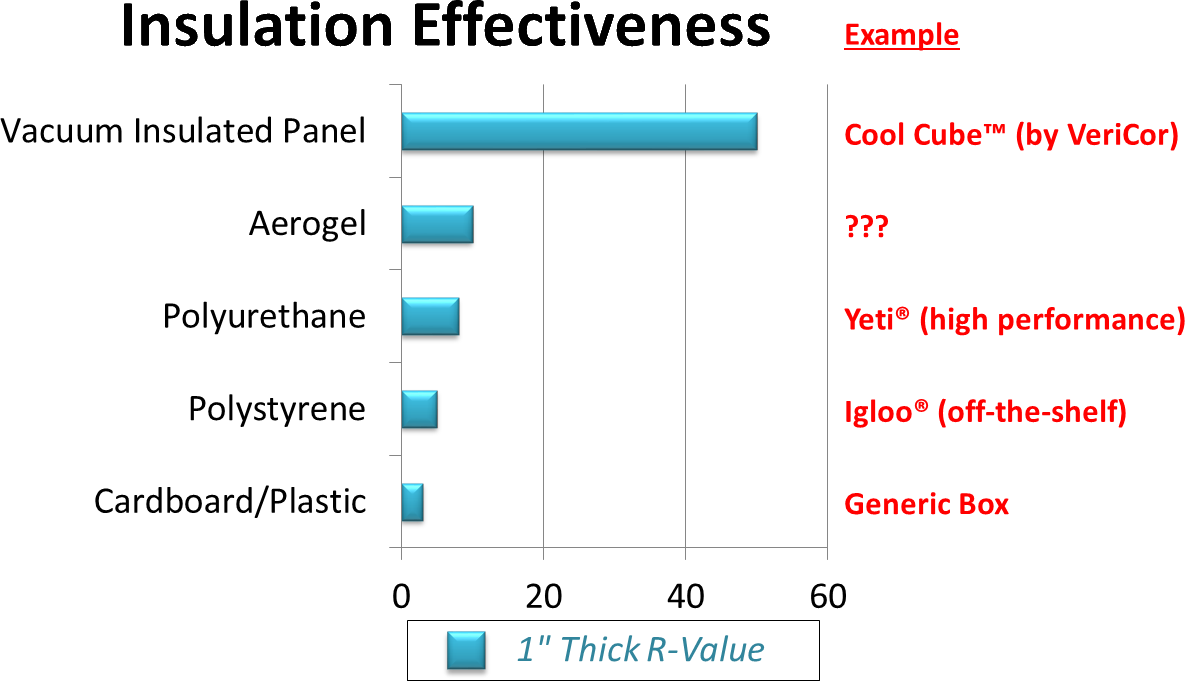
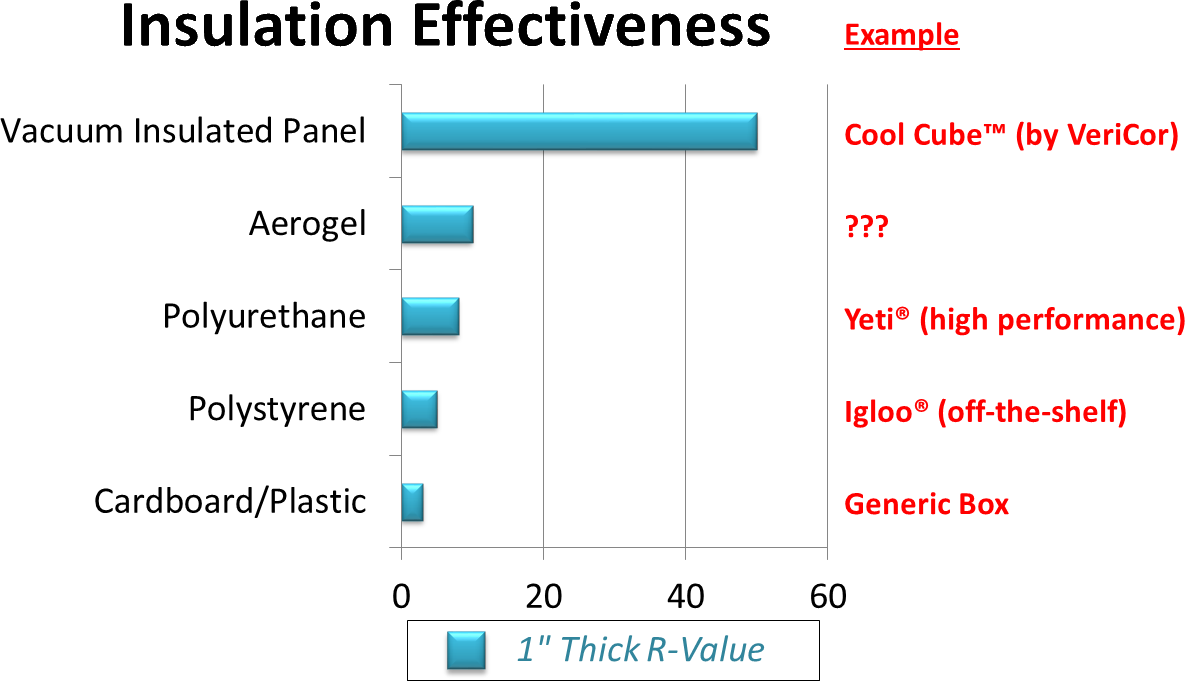
What type of insulation is in your cold chain management cooler? The insulation is the key factor in how long the temperature sensitive product will stay the correct temperature and the uniformity of the temperature throughout the product. So more importantly, what is your product worth? The higher the value, the better the insulation you should want.
The Coolant
In cold chain management the idea is to keep temperature sensitive product (vaccine, blood, medicine, etc.) within a desired temperature range. To do this there are two types of coolant systems: active (mechanical) or passive (non-mechanical). Active systems are good for long term storage, especially when electricity and space are abundant and things do not need to be moved. Yet cumbersome cords, limited mobility, bulky weight, mechanical failures, short lifespan, high total cost of ownership and maintenance are all problems associated with active systems. Passive solutions are good for backing up active systems, when mobility is needed, and/or when the electricity goes out. Although not a solution for an extended time period (more than a week), today’s passive technology can manage virtually any temperature with ease. The Coolant
Passive cooling uses natural resources to absorb or dissipate heat, with the most common being phase change material (PCM). An example of a PCM is water/ice. Use ice in or around a drink and it cools down rapidly as the ice (at 0°C/32°F) absorbs heat (from the drink and/or environment) until it is totally melted. Once melted, the temperature of the drink will quickly rise. Although PCM won’t work indefinitely, it is a reliable, simple, low-cost system to manage temperature. But how does this play into cold chain management?
If temperature sensitive product needs to be kept at 0°C/32°F and freezing is not an issue, water/ice is a good first choice as it’s cheap and easy to manage. HOWEVER, water/ice is not appropriate for any other temperature range! As stated before, ice water is at 0°C/32°F and absorbs heat from anything around it until the ice is fully melted. Once melted, the temperature quickly rises in comparison to the length of time it took to melt. For example, in a cooler full of 5°C/41°F vaccine, adding conditioned ice bottles (which are at 0°C/32°F) drives down the temperature of the vaccine by absorbing its heat – well below the 2°C minimum. This common occurrence of accidental freezing became prominent in late 2017 when a California medical center needed to re-vaccinate 23,000 patients due to its ice pack protocol. It’s also a possible reason why the conditioned water bottle technique is now only okay for emergency transport and NOT for off-site clinics, satellite facilities, or relocation of stock.
The solution? Tested, quality, engineered PCM. PCM can now be formulated to handle almost any temperature range. In other words, the freeze/thaw point can be custom made to sit right at the temperature of the product…not too hot or not too cold. Instead of frozen water bottles that are at 0°C/32°F until totally melted (driving the temperature of the cooler down), quality PCM can be made to melt at 5°C/41°F keeping the temperature of the cooler at 5°C/41°F when filled with vaccine. Instead of using dry ice (too cold) or regular ice (too warm) in a cooler containing frozen varicella, now a custom PCM that sits at -20°C/-4°F can be used to keep the varicella at -20°C/-4°F. Instead of using ice (too cold) in a cooler filled with naloxone, now a custom PCM can keep a cooler at 20°C/68°F inside a hot car sitting in the sun.
The trick is using the right PCM. Inexpensive gel packs that can be bought in bulk are no good. The thermal properties are variable, the ingredients could be toxic, and/or the durability could be poor. On the other hand, specifically engineered PCM can be made with sharp freeze/thaw points, as a non‐toxic/non‐carcinogenic mixture, being biodegradable, with good stability upon thermal cycling (no super‐cooling), and be non‐corrosive. So in general, engineered PCM has changed the game of cold chain management transport. The use of a quality PCM is safer, more efficient, and easier to manage compared to its water-based counterpart. However, it is more expensive. But again, what is your product worth?

The Ideal Combo for Cold Chain Management
Being aware of the two main components of a cold chain cooler is vital in understanding the cold chain system as a whole. What type of insulation do you want protecting your product? What type of coolant will provide a safe, controlled temperature inside the cooler?
Cool Cube™ PCM coolers integrate the best technologies of these two components. Vacuum insulated panels on all six sides of the coolers enable temperatures to last for 4 days! Quality PCM panels make packout safe and easy. To learn more about Cool Cubes™ visit, www.vericormed.com/protect.
You must be logged in to post a comment.